デジタルシフトが生み出す新たな生産現場とは?
ー 個別最適化されたプロセスで工場流れが分断されていませんか
今、製造業のデジタルシフトが大きな注目を集めています。その大きな理由の1つは、高収益なモノづくりを実現できる可能性があるからです。
日本の製造業はアメリカ、ドイツに比べてROE(Return on Equity:株主資本利益率)やROA(Return On Assets:総資産利益率)が低いことがかねてから経営上の課題となってきました。日本の製造業はこれまで現場でのカイゼンを続けてきたにもかかわらず、なかなか高収益モデルを築けず、国際競争力も低下しつつあります。
この状況を変革するために、有効なアプローチとなるのが生産プロセスを含めた企業活動全体をすべて新たな視点でとらえ直し、刷新することです。すべてのものがインターネットでつながるIoTによって、工場内の生産プロセスや物流、販売チャネルといったサプライチェーンの状況までもが、デジタルデータで瞬時に把握できるようになります。これらの情報を分析することで、「どこに無駄があるのか」「どこを改善すればよいか」といったピンポイントの現状分析と解決法の発見、さらには将来の需要予測さえも可能になります。
例えば、販売された製品の使用状況や在庫がリアルタイムにモニタリングできれば、製品企画や生産計画の精度が高まるでしょう。さらに、市場の状況などの外部データも活用できれば将来の需要予測に基づいたムダのない効率的な生産が可能になるはずです。
このように個別最適化されたプロセスで分断されていた各工程をデジタルでつなぎ、サプライチェーン全体で新たな価値を生み出していく次世代型の製造モデルが出現しつつあります。
それは進化し続けるIoT/ビッグデータ技術を活用し、生産現場となる工場内のデータ連携と分析を核に、サプライチェーンのE2E(End to End:営業活動から保守サービスまで)の情報を有機的に結合しながら、最適な生産と経営の実現にチャレンジする取り組みです。
こうした取り組みを行うことで、製造業は工場の全体最適化による生産効率の向上やリードタイムの短縮、生産・保守在庫の削減といった価値を手にし、CCC(Cash Conversion Cycle)の最小化による収益率の向上と競争力強化を獲得できるのです。
産業構造の変曲点を迎える中、製造業の次なる一手は「デジタルによる生産プロセス・サプライチェーンのE2E改革」で、現場起点で経営の改革を加速させることではないでしょうか。
ー 在庫最適化や品質のさらなる向上など課題があった日立の工場
日立では、モノづくりの再構築を具現化し、社会イノベーションに向けた経営改革を加速するための「スマートファクトリー」の実現に早くから取り組んできました。もちろんそこに至るまで、国内外で展開されている日立の工場でも、さまざまな課題がありました。
例えば、
「リードタイム短縮」…仕掛かり、作業時間、稼働状態などの状況把握に時間がかかっていた。
「多品種少量生産」…急な変更やトラブルにより、全体最適となるスケジューリングが難しい。
「過剰在庫」…部品調達や生産の拠点間調整は各担当者に依存した個別対応となり時間がかかるため、生産の平準化や部品の過剰在庫の抑止が難しかった。
「属人的作業」…段取り、組み立て、検査などの工程で属人的作業が発生し、リードタイムや品質のばらつき要因にもなっていた。
といったことはその一例です。
こうした課題を解決するため、日立はサプライチェーンにおける営業活動から受注、設計、調達、製造、物流、サービスまでのE2Eの業務プロセスを全体最適の視点で見直し、環境変化への対応スピードをさらに加速させることにしました。
具体的には、
(1)「センシング」…既存のビジネスデータや、IoTによる4M(Man:人、Material:モノ、Machine:設備、Method:手段)データを収集。
(2) 「つなぐ(統合)」…それら多様な形式のデータを簡単・スピーディーに変換してつなぐ。
(3) 「分析・見える化」…統合データベースから複雑に絡み合う要因を自動的に分析・見える化して問題を抽出。
(4) 「自動フィードバック」…その結果に対し最適なアクションを迅速に策定し、自動フィードバック。
このサイクルをすばやく回すことによって、リードタイムの短縮や在庫の削減、生産平準化といった業務全体の最適化を実現していく取り組みを開始したのです。
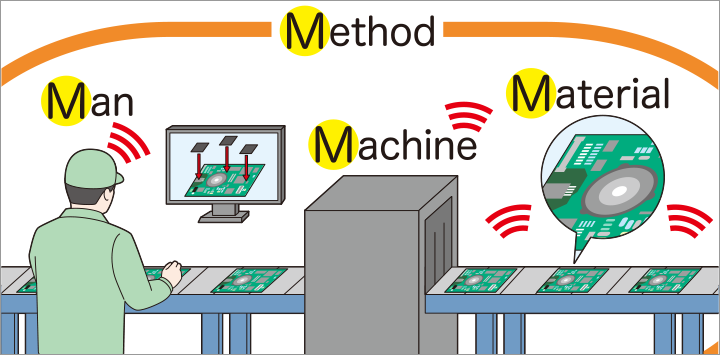
さらなる効率化を図るため日立ではIoT による4M(Man、Machine、Material、Method)データを収集する「センシング」、
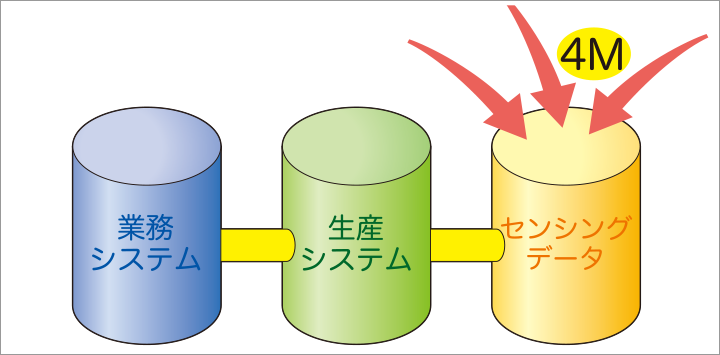
既存のビジネスデータやセンシングデータといった多様なデータを簡単スピーディーに変換して「つなぐ」、
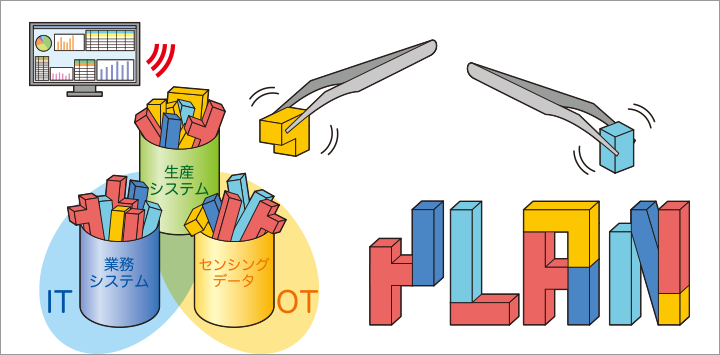
そして統合データベースから複雑に絡み合う要因を分析・見える化して「最適化」アクションを策定。
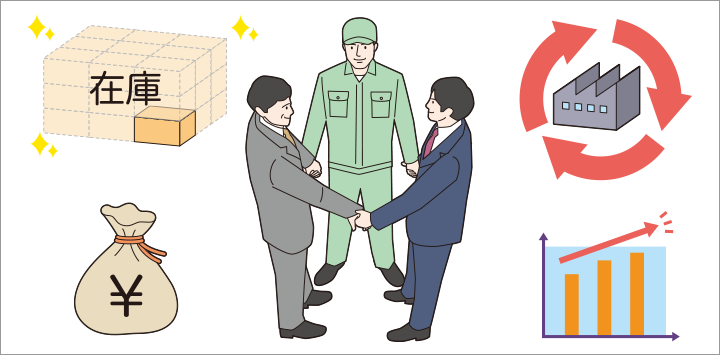
さらなるサービスレベルの向上と業務全体の最適化の実現をめざしています。
それはCCCの改善と同様に、企業がさまざまなアセット(資産・資源)をどれだけ効率的に活用し、ビジネスをしているかを測る指標の1つROAを最大化するための取り組みともいえます。
部品や生産設備だけでなく、現場で働く人の動きや、時々刻々と生み出される情報をデジタル化して共有し、さらなる有効活用を図ることで、サプライチェーンは最短の時間で最大のキャッシュフローを創出することが可能となるのです。
全体最適化、生産計画、在庫管理で大きな成果を生んだ改革の中身とは
ー デジタル改革を加速する組織的な取り組みとコア技術
こうしたE2E改革の推進には、やはりITの活用が欠かせません。そこで日立は、2007年から事業部門、研究開発部門、グループ会社が共通に使える設計基盤センタ、そして設計・生産管理のためのクラウドを整備して運用を開始しました。このセンタと各拠点をネットワークで結んで、設計ツールのライセンス、ITリソースや設計方法などを共有。現在、日立内で33の事業所とグループ会社が利用しています。
このインフラをベースに、ビッグデータ解析を始めとするさまざまなコア技術が利用可能になったことで、PoC(Proof of Concept:実証実験)の迅速な立ち上げや先行事例の共有が実現。この1年間だけでも在庫管理、生産計画、故障診断/予兆保守、設備の高稼働/長寿命化といった30件以上のテーマで400人以上がPoCに取り組んでいます。
もちろん、この取り組みを支えたものはITだけではありません。それは、日立が戦略的に行ってきた設計基準、部品や生産プロセスの共通化です。この共通化により柔軟な生産体制を確立。日立では各工場間がフレキシブルに連携した高効率生産とBCP(Business Continuity Plan)体制を構築し、受注増などに対応して、A工場で生産している製品をB工場でも生産できるようにして、全体でのライン稼働率向上や災害発生時でも安定生産を行えるようにしています。
また、核となる設計・生産管理クラウドで活用されているコア技術の代表例が、グローバルで豊富な実績を持つPentahoソフトウェアと、日立独自の人工知能技術「Hitachi AI Technology/H」(以下、AT/H)です。
Pentahoソフトウェアは、世界180ヵ国、1,500社を超える企業で使用されており、1万件以上の本番システムで稼働実績があるツールです。「データの収集・加工・統合」と「分析・可視化」という2つの機能を備え、データの流れを作図するだけで、データ収集・統合から分析・可視化までをプログラムレスで容易に実現できます。
一方のAT/Hは、リードタイム短縮や在庫の削減、品質の安定化といった目的を設定することで、インプットされたデータから自動で仮説を導き出します。人が作った仮説に頼らず、コンピュータがデータから逆推定するため、その道の専門家でも思いつかないような仮説を生み出すことができます。
人・モノ・設備・手段の情報を循環させる高効率生産モデルを確立
先進的な環境と技術を活用し、現場で大きな効果を生み出している日立のE2E改革。その工場での取り組みの具体例を、いくつか順にご紹介していきましょう。
まずは、ある事業所における「全体最適化」の事例です。
そこでは日立グループの構造改革の一環として、数年前から約8万個のRFID(Radio Frequency Identification)タグを活用し、工程の見える化によってムダを排除する「RFID生産監視システム」と、個別設計を減らして設計・調達工程での生産リードタイムの短縮を図る「モジュラー設計システム」を導入。高効率で柔軟な多品種少量生産に向けた取り組みを開始していました。
そして2016年、これまでの取り組みを一段と深化させ、E2Eの視点でサプライチェ-ンと工場の生産活動をデジタル化。新たに「作業改善支援システム」と、「工場シミュレーター」を導入しました。この4つのシステムを連携させることで、人・モノ・設備の情報を循環させる高効率生産モデルを確立しています。
具体的には、次のような仕組みになります。
「RFID生産監視システム」…各工程の進捗をリアルタイムに把握し、遅延が発生した工程に対して人員のシフトなど迅速な対策を行います。
「作業改善支援システム」…3D画像での作業指示によって作業品質を向上させるとともに作業を画像で記録。作業時間が通常よりも長くかかっている生産工程を検出し、画像分析などにより問題点を可視化し、対策・改善を行います。
「モジュラー設計システム」…上記2つのシステムに蓄積された工程改善や作業改善の結果をこのシステムにフィードバック。モジュラー設計の適用率を向上し、個別設計をさらに減らします。
「工場シミュレーター」…3つのシステムから得られた生産実績データと納期などの情報をもとにシミュレーションを実施し、最適な生産計画を提示。人員や部品などのリソースを最適に配分し、生産リードタイムを短縮するとともに、部品の早期入荷の抑制につなぎます。
このように4つのシステムで情報を循環させ、生産計画の進捗把握と対策・改善、その改善結果の製品設計へのフィードバック、より精度の高い生産計画を立案し、更なる改善の実行を繰り返すことで、生産の高効率化を図っています。その結果、代表製品*1において、生産リードタイムの50%短縮を実現しました。
*1 電力や社会産業分野向けの制御装置。その事業所で製造している製品の約20%程度を占める。
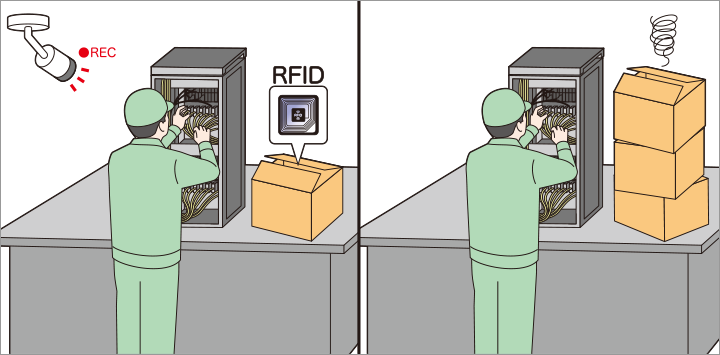
工場内でのさらなる効率性や生産性を高めるため、各工程の進捗をリアルタイムに把握し、遅延が発生した工程に対して人員シフトなどの対策を行い
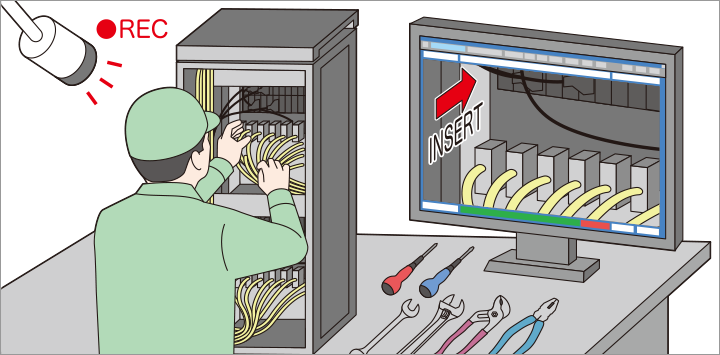
3D画像での作業指示により作業品質向上を図っています。
また、作業を画像で記録し、画像分析などにより生産工程の問題点を可視化、対策改善を行います。さらにモジュラー設計システムにフィードバックし、設計改善にも生かされます。
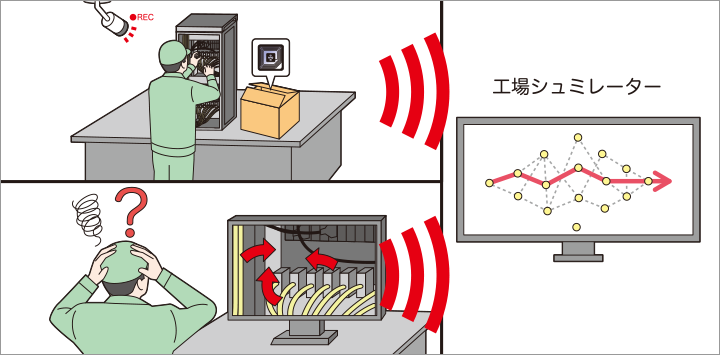
ここまでの仕組みから得られるさまざまな情報を基にシミュレーションを実施。
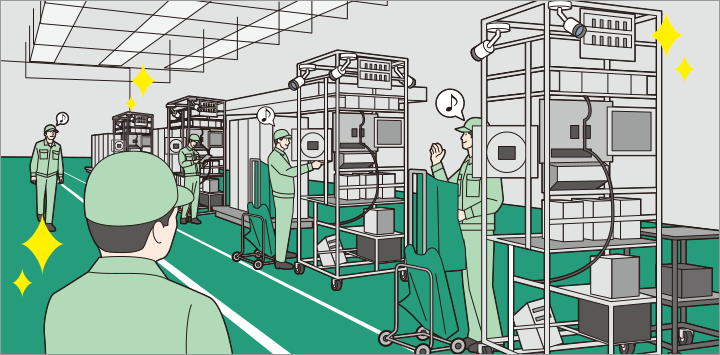
人員や部品などのリソースを最適に配分し、生産リードタイムを短縮するとともに、部品の早期入荷抑制にもつながります。
このような技術やノウハウは、日立全体での改革に横展開されています。
ー 生産計画最適化によってリードタイムを短縮
次にご紹介したいのは、「多品種混流生産ラインでのリードタイム短縮」の事例です。多品種少量生産を行う事業所では、1つのラインに多品種を混流させた生産を行ってきました。しかし生産する品種を頻繁に切り替える必要があるため、それぞれの生産ラインの作業負荷や進捗の把握が難しく、お客さまからの短納期要求や需要変動に応じた生産オペレーション全体のコントロールには課題がありました。
また、今後の全体的なモノづくりの形態としては大量生産から多品種少量生産へと変化しつつあることから、IoTを活用して現場の4Mデータをリアルタイムに収集し、生産・業務システムのデータと統合するシステムの構築により、集められた膨大なデータをPentahoソフトウェアで統合、ダッシュボードで見える化することでライン負荷、稼働状況を一目で把握できるように推進しています。
具体的には、「製品の仕掛かり数」「リードタイム」「待ち時間」といったさまざまな角度から各現場の作業実態を把握し、ボトルネックとなっている原因を抽出。さらに、「品種」、「生産順」、「作業者」などの膨大な組み合わせから高速に最適解をシミュレーションで求めてフィードバックし、PDCAサイクルを高速化、複雑な多品種混流ライン全体をリアルタイムに最適化することによって、生産ライン負荷の平準化、リードタイムの短縮をめざしています。
「生産在庫」と「保守部品在庫」を大幅に削減した施策とは
次は「生産在庫削減」と「保守部品在庫削減」の事例です。
これまで部品と半製品といった生産在庫は、営業・調達・生産の各担当者が個別最適で管理していました。そのため、担当者間での調整が難しく生産在庫を抱えるケースもありました。必要以上の生産在庫は、維持管理費用の増加やキャッシュフローの減少といったリスクにつながります。お客さまの要求や設計変更に素早く対応しながら、いかに生産在庫を最小化するかが大きな課題となりました。
その解決法として考案されたのが、Pentahoソフトウェアの統合分析ロジックを活用し、膨大な情報から、管理者が必要な情報を迅速に見つけだして在庫削減の意思決定を促す「在庫管理ダッシュボード」です。
このシステムでは、営業・設計・調達・生産それぞれのデータをタイムリーに結合し、部品ごとの在庫数と金額、過剰在庫の要因分析結果を担当者全員で共有。表示内容を見ながら、各部門が一緒になって次のアクションやその結果生じる影響について考えます。
例えば、営業はお客さまの声を反映した出荷計画になっているか、生産はそれを反映した生産計画になっているかを確認。一方、調達は発注ロットが過剰になっていないかあるいは、設計変更による部品の切替タイミングが問題ないかを確認します。このような在庫管理のPDCAを実行することにより、生産工程における在庫削減をめざしています。今後、PDCAのサイクルを月次から週次・日次へ短縮することで、さらなる在庫削減も可能になると見込んでいます。
同様に、出荷した製品(装置)の保守部品の在庫管理も問題を抱えていました。これまで日立の保守拠点では、お客さま先で稼働している製品が故障した時の緊急保守に備えて在庫に余裕を持たせて保守部品の配備を行なっていました。そのため、たまにしか使用しない部品が余剰在庫となるケースも多く、いかにお客さまへのサービスレベルを維持しながら保守部品在庫の適正化を図れるかが重要なテーマになっていたのです。
そこで考案されたのが、お客さまに納めた装置のリモート監視による稼働情報(ログ)と、各工程のデータを連携した高度なフォーキャスト運用により保守部品の配備を最適化するシステムです。
消耗数の需要予測には製品の稼働状況、設置環境、季節や地域など複数要因が絡み合いますが、AT/Hが過去のさまざまな実績データから学習し、今後の需要量を高精度に予測。その分析結果を在庫管理ダッシュボードでデータ統合し、部品ごとに「欠品」「適正」「過剰」といった在庫判定として見える化を実現。また、ロジスティクスデータも組み合わせることで保守部品在庫の最適な拠点配置についても日本地図上に分かりやすく表示します。この仕組みにより、在庫管理の最適化とサービスレベルの向上を実現しています。これにより保守部品調達の手配期間を3ヵ月から1ヵ月に短縮し、全体在庫の削減を図ることができました。
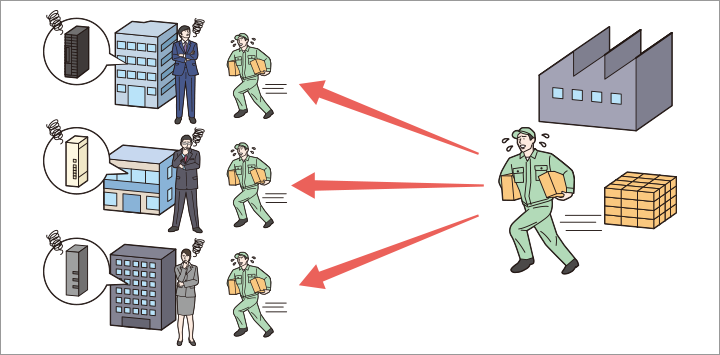
お客さまビジネスを支えるシステムの安定稼働のため、緊急保守に備え、在庫に余裕を持たせた保守部品の配備を行っていました。
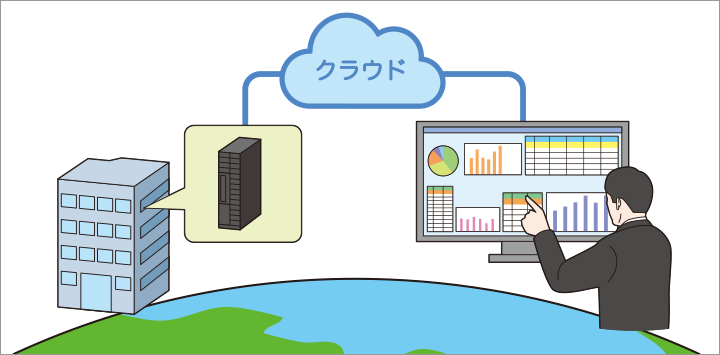
日立では課題解決のために、お客さまに納めた装置のリモート監視および保守部品配備の仕方を最適化するシステムを構築。
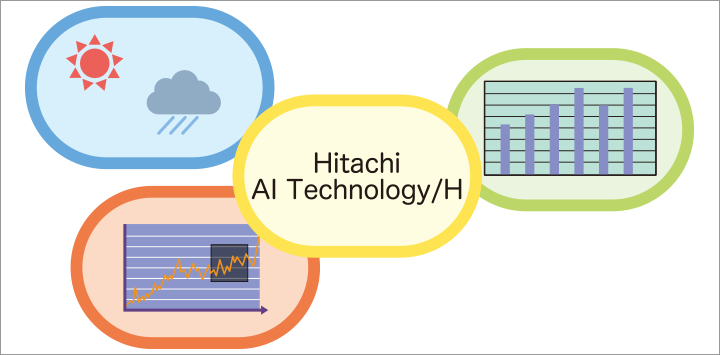
それらの情報をもとにAIが今後の需要量を高精度に予測することで
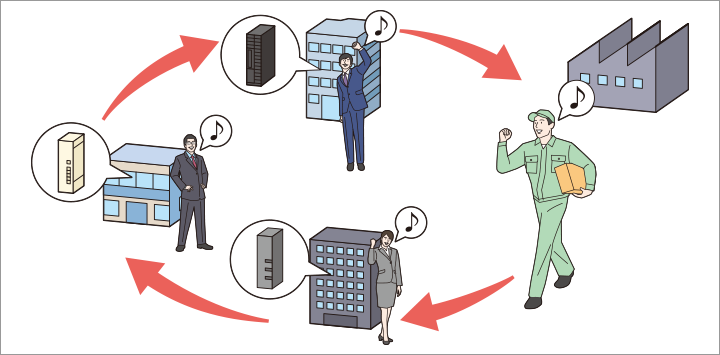
在庫管理の最適化とサービスレベル向上を実現します。
自社での取り組みに加え、お客さまとの協創で改革を拡大
ー 日本の製造業の「底力」を呼び覚まし、新しい時代を創りたい
サプライチェーン改革、コスト構造改革、品質確保・向上などは多くの製造業に共通する経営課題であり、これまでに紹介したような取り組みを検討している企業も少なくないでしょう。そこで、日立では自社での取り組みに加え、お客さまとの協創活動も推進しています。
「ダイセル式生産革新」で世界的にも有名な化学製品メーカー、ダイセルとの取り組みはその一例です。共同で開発した「画像解析システム」は、作業者や設備、材料加工の状態を5種類のカメラで撮影し、専用アルゴリズムで解析することで、ミスや不具合の予兆を見つけ出し、生産ラインのマネージャーに通知します。これにより、品質保証を生産ロット単位の「代表点管理」から、製品ごとに連続監視できる「全点管理」への移行を実現。工程内保証率を高めることに成功し、今後もさらなる品質や作業効率の改善が期待されています。
このようなお客さまとの協創や自社検証を行ってきた数々の成功事例を、デジタルソリューションとして提供する取り組みも強化しています。高効率生産モデルや、ダイセルと共同開発した画像解析システムはすでにIoTプラットフォーム「Lumada」においてテンプレート化されています。これを利用すれば、お客さまの経営課題や業務課題を迅速に解決することも可能になるはずです。
製造業は今、確実に新しい時代への入り口に立っています。
それぞれの企業が持つ「底力」を呼び覚まし、新たな世界の潮流へと乗せるための第一歩を、日立とともに踏み出して行きませんか。
関連リンク
・ダイセルインタビュー「人にやさしいモノづくり」の真髄とは
・Lumada
シリーズ紹介
楠木建の「EFOビジネスレビュー」
一橋ビジネススクール一橋ビジネススクールPDS寄付講座特任教授の楠木建氏の思考の一端を、切れ味鋭い論理を、毎週月曜日に配信。
山口周の「経営の足元を築くリベラルアーツ」
山口周氏をナビゲーターに迎え、経営者・リーダーが、自身の価値基準を持つための「リベラルアーツ」について考える。
協創の森から
社会課題の解決に向けたビジョンの共有を図る研究開発拠点『協創の森』。ここから発信される対話に耳を傾けてください。
新たな企業経営のかたち
パーパス、CSV、ESG、カスタマーサクセス、M&A、ブロックチェーン、アジャイルなど、経営戦略のキーワードをテーマに取り上げ、第一人者に話を聞く。
Key Leader's Voice
各界のビジネスリーダーに未来を創造する戦略を聞く。
経営戦略としての「働き方改革」
今後企業が持続的に成長していくために経営戦略として取り組むべき「働き方改革」。その本質に迫る。
ニューリーダーが開拓する新しい未来
新たな価値創造に挑む気鋭のニューリーダーに、その原動力と開拓する新しい未来を聞く。
日本発の経営戦略「J-CSV」の可能性
日本的経営の良さを活かしながら利益を生み出す「J-CSV」。その先進的な取り組みに迫る。
ベンチマーク・ニッポン
日本を元気にするイノベーターの、ビジョンと取り組みに迫る。
デジタル時代のマーケティング戦略
マーケティングにおける「デジタルシフト」を、いかに進めるべきか、第一人者の声や企業事例を紹介する。
私の仕事術
私たちの仕事や働き方の発想を変える、膨らませるヒントに満ちた偉才たちの仕事術を学ぶ。
EFO Salon
さまざまな分野で活躍する方からビジネスや生活における新しい気づきや価値を見出すための話を聞く。
禅のこころ
全生庵七世 平井正修住職に、こころを調え、自己と向き合う『禅のこころ』について話を聞く。
岩倉使節団が遺したもの—日本近代化への懸け橋
明治期に始まる産業振興と文明開化、日本社会の近代化に多大な影響を及ぼした岩倉使節団。産業史的な観点から、いま一度この偉業を見つめ直す。
八尋俊英の「創造者たち」~次世代ビジネスへの視点~
新世代のイノベーターをゲストに社会課題の解決策や新たな社会価値のつくり方を探る。